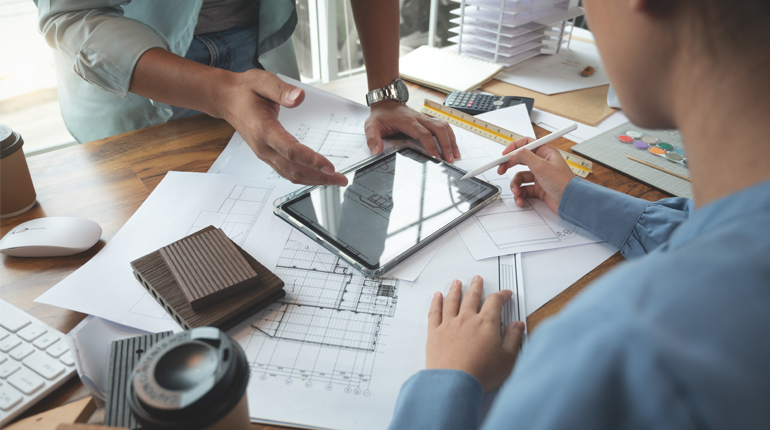
In construction, clients will award the job to the perceived best bid. Bids are created through estimates and predict both the total scope of a job and its cost to complete.
This means that a single mistake or miscalculation during the estimating process can easily lead to lost revenue. Underestimated materials and quantities can lead to expensive delays and budget overruns. And overestimation could lead to waste if orders were fulfilled before the error was detected. Because of this, accuracy in the estimating process – particularly when completing the construction takeoff – is essential.
In order to ensure the accuracy of an estimate, contractors must create a comprehensive, precise takeoff before they can even begin to appropriately cost out a project.
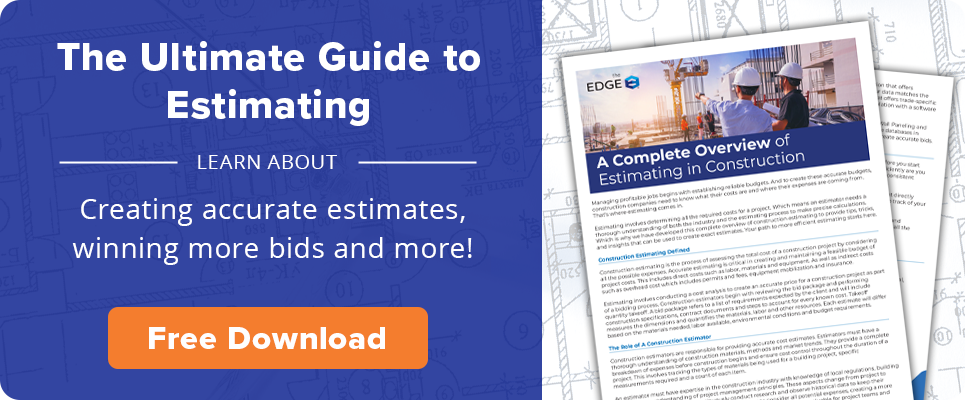
Construction Takeoff Comes Before Construction Estimating
You may be wondering what the difference is between a takeoff and an estimate. Are they interchangeable terms? Can you do one without the other? Do they have to be completed in any specific order?
The answer:
Takeoff and estimating go hand-in-hand. You can’t really have one without the other. The takeoff comes first. It results in a detailed, itemized list of materials and quantities. Estimators use this list to complete the estimate. The estimate, at its core, assigns costs to each of the items on the takeoff “list.”
So, while takeoffs and estimates are separate tasks, they are dependent on each other. An accurate takeoff is essential to an accurate estimate in the same way that an accurate estimate is essential to an accurate bid.
Imagine the takeoff and estimate like a hybrid shopping list and budget that forms the basis for a project’s execution. The takeoff forms the shopping list, and the estimate entails the prices assigned to each item. For example, if we buy $1.50 worth of apples, then the apples would go on the takeoff, and the $1.50 would go on the subsequent estimate.
The Definition of Construction Takeoff
Construction takeoff is the process through which an estimator will quantify, or count, the materials, labor, equipment and other elements required for a construction project. Takeoff must be accurate so estimators can assign appropriate costs.
Without a takeoff and estimate, it’s impossible to provide an accurate bid to the client. If you simply guesstimate the price it will cost to complete a project without actually going through the steps of the takeoff and estimating process, you’re liable to exclude imperative facets of a project from your final proposal.
For example, how will you know how many gallons of paint it will take to paint the interior walls of a new library unless you measure the walls? This is where takeoff comes into play.
To complete a takeoff, estimators must scrutinize and analyze architectural and engineering plans, pull pertinent information, and transcribe that information into a complete list of items and quantities that will be used for the takeoff.
For example, let’s say you’re beginning construction on a new library. The library will be a two-story building and is slated to be 2,640 square feet. In order to begin the takeoff, estimators will use this information to begin figuring out how much flooring will be needed to fit the floor plan.
Why Construction Takeoff is Important in the Bidding Process
Construction is a highly competitive field – especially when it comes to bidding government jobs. An accurate and effective takeoff and estimate are essential in order for contractors to even be considered for work.
When contractors take the time to complete a comprehensive construction takeoff before diving into their estimate, they’re ensuring that they’re presenting an accurate bid to the consumer. This, in turn, helps contractors to maintain a healthy profit margin and positive consumer relations.
When a takeoff is not completed, contractors risk submitting bids that are too high or too low.
When a takeoff is well-executed and accurate, contractors are granted a competitive edge, ultimately helping them to secure jobs.
An accurate takeoff will also help estimators throughout a project’s lifetime. Oftentimes, contractors will use the quantities in the bid that were calculated by the takeoff to order materials. Once a project is complete, estimators will compare numbers from the takeoff and estimate with the actual quantities that were used to complete the project.
A Construction Estimator’s Role in Construction Takeoff
Estimators are not just responsible for creating estimates; they’re responsible for completing the takeoff for a project as well.
Estimators are typically given blueprints and project plans that they are expected to use to complete the takeoff. They will need to comb through these documents and take measurements that they will eventually use to determine how much of each material is required to complete a job.
Certain traits will benefit estimators, including an eye for detail and a robust understanding of construction materials, construction techniques, and local rates for both material and labor. Estimators must also have the ability to measure accurately and to transcribe their measurements to the scale presented on the given blueprints.
The Process of Takeoff in Construction
When takeoff is broken down, estimators can look at each segment if their measurements ever go array and determine exactly where they went wrong.
- Step 1: Evaluation – Contractors must begin each bid by studying the project scope. They must analyze the blueprints, paperwork, and other materials provided to them by the bid granter.
These materials will help them visualize the project as a singular whole and determine which materials will be used in what quantities.
Those opting for manual takeoff will require physical copies of these documents for manual review. If using a digital construction takeoff solution, scanned versions would be most appropriate, as they can be uploaded into the software.
- Step 2: Start the Count! – After the initial evaluation, estimators will get into the more nitty-gritty aspects of the takeoff. Using the blueprints and project plans as a guide, estimators will begin to count the items that are required to execute and complete the project.
Estimators estimating manually will need to manually count each item by hand, while those using digital takeoff solutions will only need to review the final results for accuracy.
- Step 3: Measure, Measure, Measure! – After all required items have been accounted for, estimators will need to measure quantities needed, paying special attention to the scale used on the blueprints.
For items like drywall, paint, and insulation, estimators will need to calculate square footage for the areas where these materials will be applied. For items like steel beams and gutters, they’ll need to calculate linear footage.
Manual takeoffs will hinge on scale rulers, whereas those using software can rely on automated programs to generate the required measurements.
- Step 4: Calculate Quantities – After you have completed both the count and subsequent measurement, the exact quantities required for each material must be determined. To determine these quantities, combine your list of needed materials with the measurement calculations.
- Step 5: Determine Expenses – The last step in the takeoff process requires estimators to put a price to all the items it will take to complete a given project.
Estimators completing the takeoff by hand may rely on a combination of supplier quotes and industry expertise to determine expenses. Those using the software can use the available digital tools to access pricing databases that pull their information from local supply houses.
What’s Included in a Construction Takeoff?
A well-done takeoff is all-inclusive, meaning it looks at a project on the micro-level, analyzing everything from the number of nails needed to the total amount of drywall required. Nothing should be left to chance.
When completing a takeoff, estimators should analyze:
- Materials: Construction takeoff should reflect each specific material that will be required to complete a project.
And Their Quantities: It’s important that estimators don’t just account for each separate material being used but that they account for the amount of every material used.
- In Practice: Items you may put in the “materials” section of your takeoff include concrete, steel beams, roofing tiles, insulation, and bricks. Every brick must be accounted for, as must the length of each gutter included. Every sheet of drywall should be counted individually. When completing a takeoff, it’s imperative no item goes overlooked.
- The Why: An estimator’s ability to accurately measure these elements forms the foundation of an accurate takeoff. These quantities will become the basis of the estimate.
- Labor: What are materials without a crew to turn them into structures? When completing a takeoff, it’s important to remember that it’s not just all about counting the materials, it’s about taking into account the skilled labor that will ultimately bring those materials together to form a singular unit, be it a house, bank or public library.
- In Practice: Be sure to figure the approximate labor hours needed for everything, including any tear-offs, clean ups and installations. The takeoff will calculate how many workers are needed and how many labor hours they’ll be working. Payroll costs will be assigned to labor hours in the estimating stage.
- The Why: In addition to helping you bid the project, this will assist project managers in allocating resources effectively and planning out work schedules throughout the project’s duration.
- Equipment: When completing a takeoff, it’s important to identify the equipment that will be used to complete the project.
- In Practice: Necessary equipment should be considered for each stage of the project, including excavation, concrete pouring, and bulldozing.
- The Why: Ensuring the “equipment” aspect of the takeoff is accurate will not only ensure there is enough budget available to complete the project but will help to ensure the correct machines are on-site at the correct times, preventing delays and disruptions.
- Miscellaneous: Other items that must be accounted for include insurance, rent, and other general overhead items.
- In Practice: Necessary equipment should be considered for each stage of the project, including excavation, concrete pouring, and bulldozing.
- In Practice: Be sure to figure the approximate labor hours needed for everything, including any tear-offs, clean ups and installations. The takeoff will calculate how many workers are needed and how many labor hours they’ll be working. Payroll costs will be assigned to labor hours in the estimating stage.
Remember, a truly comprehensive construction takeoff will encompass a scope far beyond this list of items. It will require the estimator to have a thorough and complete understanding of the project’s complete building plan. Keep in mind that you’re never in it alone: modern tech has truly transformed and altered the takeoff process with digital software that simplifies the process and allows for easy cross-team collaboration.
A Construction Takeoff Example
Let’s you’re bidding a job to build a new library for the city of Strongsville, Ohio.
- Step 1: Evaluation – Study the blueprints and project plans given to you by the architect. If possible, schedule a meeting with the architect or planning team to ask clarifying questions about the scope of the project and learn what materials the city may provide.
- Step 2: Start the Count! – Using the blueprints and project plans as a guide, count the individual items that will be needed to complete the project. This will include everything from flooring and drywall to shingles and gutter downspouts. For the sake of this example, let’s say we only need flooring tiles, carpet, nails, and bricks to complete this project. This brings our count to three.
- Step 3: Measure, Measure, Measure! – After all required items have been accounted for, measure the quantities needed. You will need to pay close attention to the scale on the blueprints to ensure your numbers are correct. Let’s say we end up needing 1,250 square feet of flooring, 2,000 nails, and 8,560 bricks to complete this project.
- Step 4: Calculate Quantities – Combine your list of needed materials with the measurement calculations. When we combine these lists, we see that we need 500 square feet of flooring tiles, 750 square feet of carpeting, 2,000 nails, and 8,560 bricks.
- Step 5: Determine Expenses – Next, we’ll put a price to our four items. In order to find these prices, we’ll reference supplier quotes and industry expertise. Let’s assume each square foot of flooring tile costs $5, each square foot of carpeting costs $8, each nail costs $0.50, and each brick costs $1.50. This means we’ll need $2,500 worth of flooring tiles, $6,000 worth of carpeting, $1,000 worth of nails, and $12,840 worth of bricks. This brings our total material cost estimate to $22,340.
Construction Takeoff Variations
Like most things in construction, there isn’t a single, one-size-fits-all approach to construction takeoff. There are many methods available, and estimators should play to their strengths when choosing the best approach for them. The four primary methods include manual, digital, 3D, and hybrid.
- Manual Takeoff
- Definition: Manual takeoff is the “old-school” approach to completing a takeoff.
- How-To: To complete a manual takeoff, the estimator will, by hand, review the architectural and engineering plans they were given for a project. From there – using pen-and-paper or spreadsheets – the estimator will record the measurements and quantities.
- Considerations: This method is considered to be labor intensive but is favored by many contractors who feel they can “get to know a job” better by completing the estimate manually.
- Digital Takeoff
- Definition: Digital takeoff first entered the industry in the early 1990s and became fairly commonplace by the 2000s. Digital takeoff allows estimators to complete takeoffs digitally using specialized software.
- How-To: Digital plans require estimators to use industry-specific software. Estimators must import digital plans and use on-screen measurements to calculate quantities.
- Considerations: Digital takeoff software typically expedites the takeoff process significantly from the pen-and-paper method – it also helps to reduce the occurrence of errors when completing the takeoff.
- Three-Dimensional Modeling (3D)
- Definition: This method utilizes 3D models to help estimators extract quantities and measurements directly from a digital model.
- How-To: This software helps estimators create a 3D takeoff and estimate. The software creates geometrical and non-geometrical information that allows estimators to further analyze the scope of the project and easily identify potential structural concerns.
- Considerations: 3D modeling helps contractors see projects holistically. With this method, accuracy is enhanced, and estimators are given a better visualization of complex structures.
- Hybrid Methods
- Definition: A cross between manual, digital, and 3D estimating.
- How-To: We don’t live in a black-and-white world, and neither do estimators. In many cases, a hybrid approach will be used over a strict manual-, digital- or 3D-only estimating process. In order to complete a hybrid takeoff, estimators will combine a number of takeoff methods in order to fully understand a project’s complexity and determine what must be put in place to complete a project.
- Example: An estimator might choose to complete a digital takeoff for the majority of a project’s components but then utilize a manual takeoff method for the elements of the project that require extra attention.
Why Accuracy is Imperative in Construction Takeoff
Most contractors are familiar with the adage “measure twice, cut once.”
This sentiment is extremely relevant in construction takeoff.
When estimating a project, the smallest measurement error or mis-prescribed quantity can lead to project delays, cost overruns, and other issues. A successful project is built on the foundation of an accurate takeoff, which minimizes the risk of unforeseen delays and ensures a project stays within the set budget and on the correct schedule.
The Top Takeoff Tips for Every Estimator
Even with experience, venturing into a takeoff can be unnerving, especially if you’re bidding for jobs that have a scale larger than you’re accustomed to. Just remember these tips:
- Have a quick turnaround time: We live in a fast-paced digital age, and people have gotten used to having information available at their fingertips. Whether you’re bidding on a private or a public project, it’s never a bad idea to get your estimate in before the competition. Doing so gives you a slight competitive edge and keeps your company name at the front of the consumer’s mind.
- Familiarize yourself with resources: The latest takeoff software may be your new best friend when completing new and complex takeoffs. It may be worth exploring what takeoff software is available for your industry. For contractors in the acoustical, flooring, drywall, painting, EIFS, roofing, fireproofing, wall panel, and waterproofing fields, The Estimating Edge is a great choice.
- Be a collaborator: Ongoing and effective communication with your crew will help to ensure your takeoff and subsequent estimate align with the team’s abilities and the project’s overall objectives.
Software For Construction Takeoff
There are a wide variety of software tools available to help simplify takeoff. For example, takeoff software was created to automate the measuring and help estimators digitally assess and calculate quantities. This software will typically take the information garnered during a takeoff and turn it into an estimate, automating the pricing process and generating detailed reports.
Construction takeoff software streamlines the takeoff process – turning something that traditionally can take hours to do with pen and paper and finish it in minutes. The software also helps contractors to mitigate the danger of making costly errors in calculations.
Contractors who work in the roofing and interior trades should consider The EDGE®. The EDGE offers trade-specific takeoff and estimating for contractors. The EDGE’s software – which offers trade-specific, customizable databases – has helped thousands of estimators create accurate bids.
See How Construction Takeoff Software Can Make A Difference For You!
Starting with the initial review of project plans and ending with the itemized list of quantities, a takeoff lays the groundwork for a project’s lifecycle. Ensuring this list is accurate is essential to ensure projects are completed efficiently and within budget.
Specialized takeoff software takes the grunt work out of completing takeoffs and leaves less room for error than traditional methods. When estimators can complete accurate bids quickly, it increases their chances of winning a higher volume of quality jobs. Takeoff software can help estimators move forward with confidence, knowing they’re submitting an accurate bid to the consumer.
Whether you choose to perform takeoffs and estimates manually or with software, we hope this guide has been a helpful tool in your estimating journey.